Schweißtechnologien
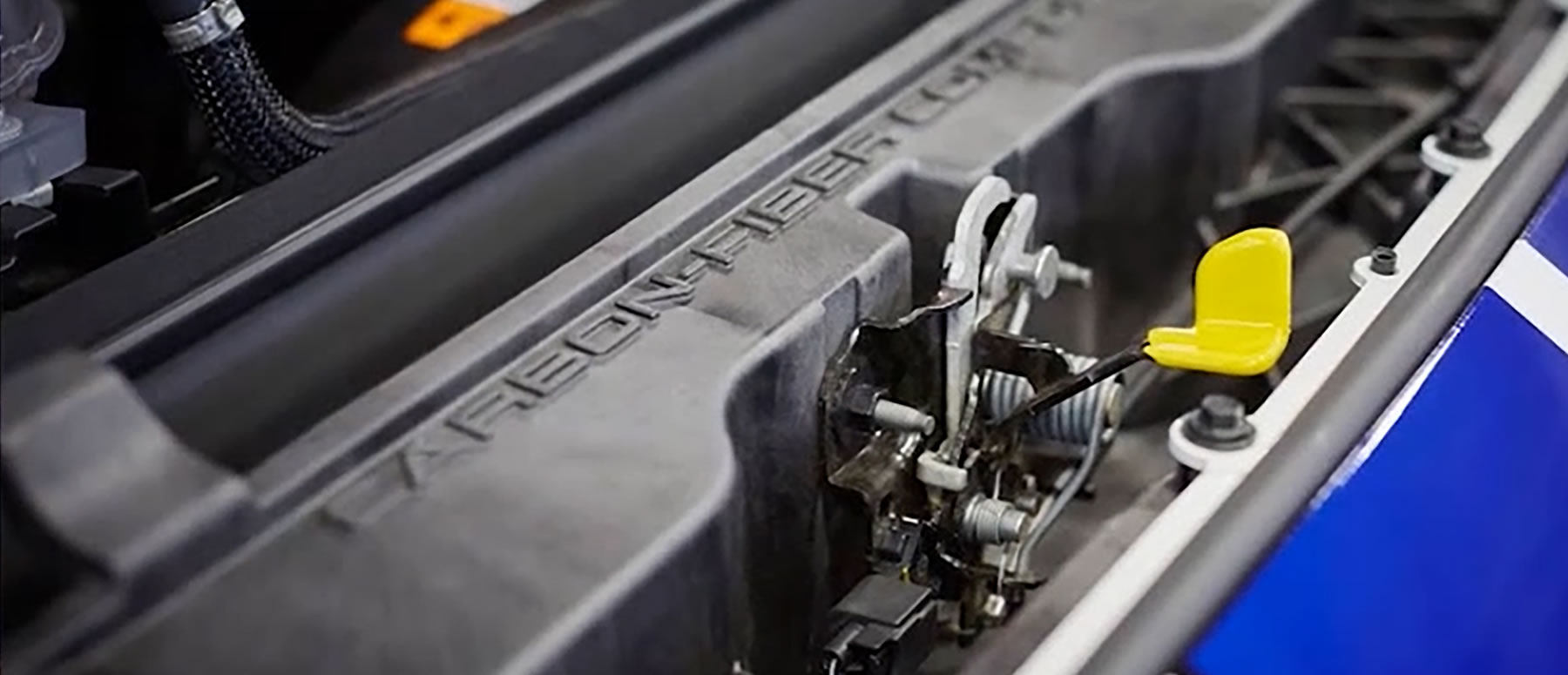
Prozessinnovation
Bei Magna setzen wir die neuesten Schweißtechnologien ein. Das hilft unseren Kunden dabei Kosten zu sparen, die Qualität zu verbessern und ihre Fahrzeuge leichter zu machen.
Resistive Implantwelding
Kostengünstiges Schweißen ohne Klebstoffe
Das Zusammenfügen von zwei oder mehreren Kunststoffteilen zu einer Schweißnaht oder Verbindung ist bei der Herstellung von Automobilteilen häufig erforderlich. Mit zunehmendem Einsatz von Kunststoffen bei Automobilanwendungen steigt der Bedarf an Möglichkeiten, solche Komponenten miteinander zu verschweißen. Das resistive Implantwelding kann verwendet werden, um Materialien mit Hilfe von elektrischem Strom zu einer Kastenprofilkonstruktion zu verbinden. Es ist ein kostengünstiges und schnelles Verfahren zum Verbinden oder Schweißen von energiearmen Substraten ohne Klebstoff.
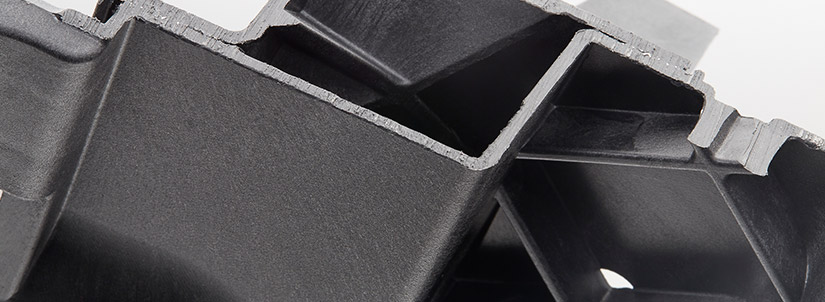
Prozess-Effizienz
Das resistive Implantwelding ist eine einfache Technik, die auf fast alle Thermoplaste angewendet werden kann. Die Schweißzeiten können relativ kurz sein, typischerweise unter 60 Sekunden für die meisten Anwendungen, was zu einer höheren Prozess-Effizienz führt.
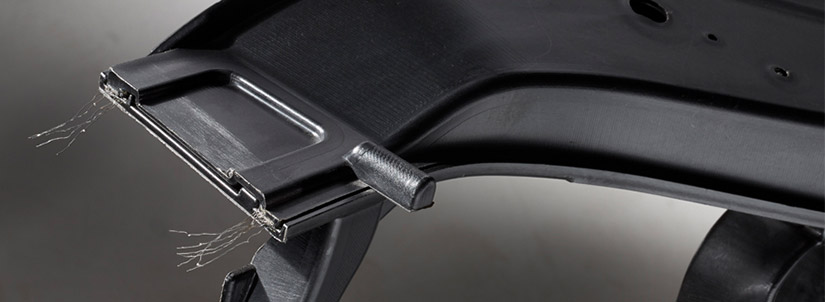
Kostengünstig
Der Verzicht auf Stanz-, Werkzeug- und Montageeinrichtungen führt zu Kosteneinsparungen für den OEM.
Torsionales Ultraschallschweißen
Präzise Verbindungstechnologien für Stoßfängeraufbauten
Das torsionale Ultraschallschweißen verbindet thermoplastische Olefine (TPO) bei der Herstellung von Stoßfängern. Eine Maschine schwingt mit hoher Frequenz und erzeugt Reibung, die dazu führt, dass zwei TPO-Komponenten, wie z. B. eine Abdeckung und eine Halterung, präzise miteinander verschmelzen. Magna ist das erste Unternehmen, das torsionale Ultraschallschweißen zur Verbindung von TPOs bei der Herstellung von Stoßfängern einsetzt.

Gewichtsreduzierung
Das torsionale Ultraschallschweißen funktioniert gut bei dünnwandigen Werkstoffen und erfordert keine Verdickung. Mit diesem Verfahren kann Magna eine Massereduzierung von etwa 10 Prozent im Vergleich zu einem herkömmlichen Wandmaterial erreichen. Aus diesem Grund kann das torsionale Ultraschallschweißen den OEMs bei ihren Leichtbau-Bemühungen helfen - eine Priorität bei der Erfüllung immer strengerer globaler Emissionsnormen.
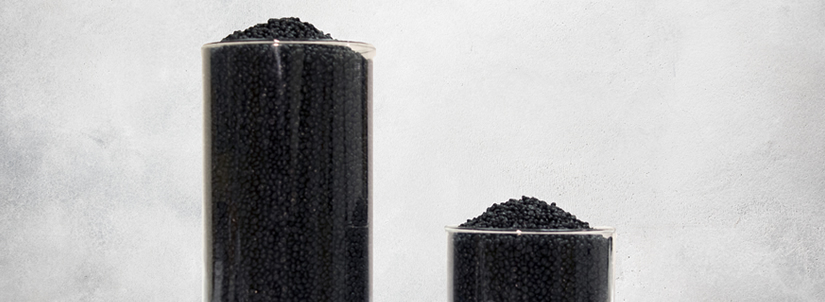
Materialreduzierung
Gewichtseinsparungen durch das torsionale Ultraschallschweißen führen zu Kosteneinsparungen durch reduzierte Materialkosten.
Laserschneiden & -schweißen
Mehrwert schaffen durch Prozessverbesserungen
Magnas Laserschneid- und -schweißverfahren bieten größere Flexibilität bei der Herstellung von Teilen mit geringerem Volumen und ermoglichen Gewichtseinsparungen durch den Einsatz eines dünnwandigen Bauteils. Außerdem werden keine herkömmlichen Stanz-/Schweißmaschinen mehr benötigt, was zu einer Investitions- und Platzersparnis führt.
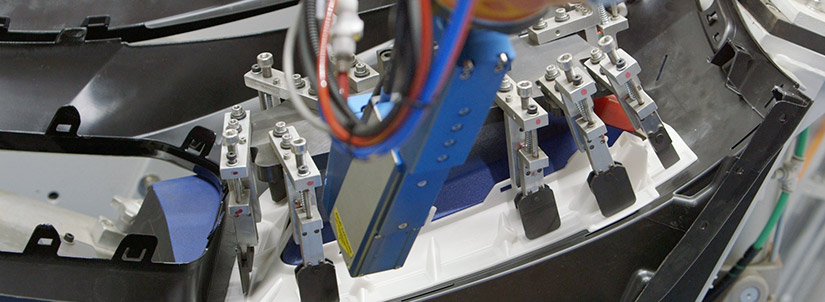
Flexible Fertigungsmöglichkeiten
Das Laserschneiden und -schweißen bietet flexible Fertigungsmöglichkeiten, wenn Nachbearbeitungen erforderlich sind. Lasergeräte können mehrere Programme mit geringerem Volumen unterstützen und mehrere zugeordnete Stanz- und Schweißzellen ersetzen.
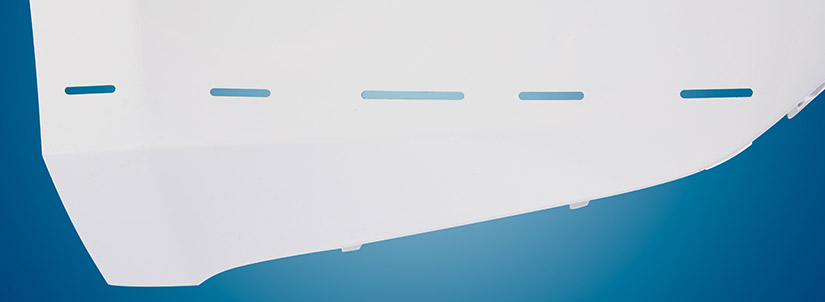
Laserschneiden
Durch die fortschrittliche Laserschneidtechnologie erhöht sich die Flexibilität durch die Zelle, da die Stempel-/Matrizengrößen nicht begrenzt werden. Das Laserschneiden schafft die Möglichkeit, die Lochgrößen mit einfachen Programmänderungen zu ändern, anstatt weitere Maschinen für eine andere Lochgrößen vorzuhalten.
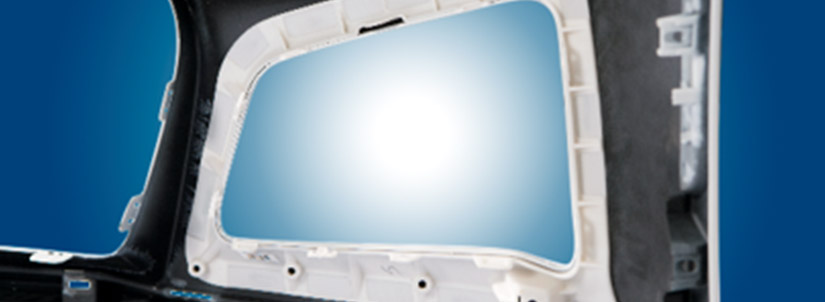
Laserschweißen
Die fortschrittliche Laserschweißtechnologie ist in der Lage, dünnere Wandstärken ohne Durchlesen zu schweißen, was zu einer Masseeinsparung bei der Gesamtmontage führt. Sie ermöglicht es den Herstellern, weniger Schweißfläche zu nutzen und höhere Abzugskräfte zu erzielen. Dies reduziert den Platzbedarf der Halterungen und führt zu einer besseren Verpackungsfähigkeit, da für das Laserschweißen kleinere Flansche benötigt werden.